Cleanrooms
Work processes that require clean rooms and controlled environments get optimal conditions with our individual, reusable and easy-to-clean MATADOR clean rooms for companies.
What is a cleanroom?
A cleanroom is a specialized environment, typically used for research or production, that maintains strict standards for cleanliness and particle freedom.
Most cleanrooms installed today (over 90 percent) are positive pressure rooms that are categorised according to ISO 14644-1 2015 cleanroom classifications, which ranks cleanrooms according to the number of particles per cubic meter by micrometre size.
This is an effective way of classifying overpressure cleanrooms – and indicating how “clean” they are – because positive pressure rooms are designed to expel air and any particles that may arise in them.
This is in contrast to negative pressure rooms, which are designed to trap contaminants in the room – a useful operation when dealing with infectious diseases, pathogens, or other biological and toxic hazards that you don’t want to release from a controlled environment.
Skov Industri offers both overpressure cleanrooms and underpressure cleanrooms via our MATADOR Cleanroom solutions, including:
- ISO 8, ISO 7, ISO 6 og ISO 5 cleanroom
- GMP A, B, C og D cleanroom
- cGMP cleanroom
- USP cleanroom
And we make sure machines and equipment can get into the cleanroom even after it’s built.
The sustainable Clean room solution
Das nachhaltige Reinraum System
Overpressure – Cleanroom
This is how pressure chambers work
To understand ISO positive-pressure cleanroom classifications, one first needs to understand how these cleanrooms work.
The clean air in a pressurised cleanroom is produced by drawing air into the cleanroom through a series of HEPA (High-Efficiency Particle Air) and/or ULPA (Ultra Low Particulate Air) filters. This provides a clean air environment and creates pressure in the cleanroom.
With air pressure in the room greater than the pressure in the surrounding environment, the air inside the positive pressure cleanroom is subsequently pushed out of the room through ventilation ducts. With this, the pollutants leave due to processes carried out inside the room. At the same time, the higher pressure inside the room stops pollutants from entering the room via exit ventilation ducts.
Classifications of overpressure rooms
With purified air being drawn in and pollutants being pushed out, positive pressure cleanrooms are classified according to the concentration of airborne particles inside them and the size of those particles – the goal is to minimise the number and size of particles in a cleanroom through continuous pressure and frequent air exchange.
The ISO standard for cleanroom classifications 14644-1, introduced by the International Organization for Standardization, has been in force since 2001. It classifies cleanrooms by cross-referencing the size of the measured particles (e.g. 0.5 μm) with the maximum number of particles of that size per m3 that can be accepted in a cleanroom of that type.
ISO 14644-1 Cleanroom classifications
ISO cleanroom classifications are largely consistent with the older US Federal Standard 209, which was in
effect from 1998-2001. Although it has been officially out of use for years, it is still widely cited and can be
easily cross-referenced with ISO classifications. Note that ISO 14664-1 is given in m3
Watch video about Cleanrooms
Requirements for ventilation, ACH
Other classifications of cleanrooms
In addition to keeping the concentration of airborne particles below a certain limit, cleanrooms for microelectronic installations must also take care of the air change rate (ACR) according to an addendum to the ISO 14644-1 standard. This factor is also becoming important for medical and pharmaceutical manufacturing.
ACR is measured in air changes per hour (ACH), which can be determined by measuring the total airflow volume supplied to – or vented from – the cleanroom.
Almost all ISO classes can be correlated to a recommended ACH range. Finding the correct ACH for an application will depend on a variety of factors, including the number of employees in a cleanroom, the processes used inside the cleanroom, and the typical frequency of entries and exits from the cleanroom.
As a result, we always work closely with the ventilation providers.
ACH areas for ISO Cleanroom classifications
Rule of thumb for number of air changes per hour according to ISO 14644-1 classes
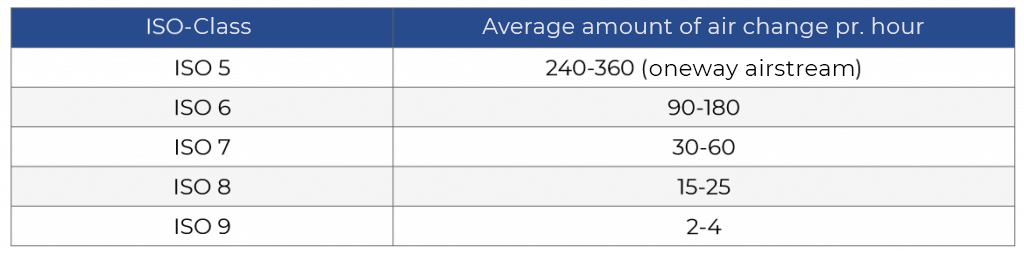
Choosing the right cleanroom is a complicated but important decision for any company that needs to maintain cleanroom standards and controlled environments in its production environment.
Read more about cleanrooms at our learning centre here
Skov Industri offers both overpressure cleanrooms and underpressure cleanrooms via our MATADOR Cleanroom solutions.
Contact us and we can discuss the best way to meet your cleanroom needs – as well as your general production requirements.