Cleanroom qualification
Cleanroom qualification ensures that cleanrooms meet strict standards for cleanroom classes and layout. Through thorough testing and documentation, it is guaranteed that the cleanroom maintains the necessary cleanliness and functionality. Important for industries such as pharmaceuticals and electronics, where precision is essential.
What is cleanroom qualification?
Cleanrooms are classified according to the purity of the air in them. The clean room class is the cleanliness level that the room complies with, according to the amount and size of particles per volume of air. The primary authority is the ISO classification system ISO 14644-1. This standard includes these cleanroom classes: ISO 1, ISO 2, ISO 3, ISO 4, ISO 5, ISO 6, ISO 7, ISO 8 and ISO 9.
ISO 1 is the “cleanest” class and ISO 9 is the “dirtiest” class. ISO 9 is still cleaner than an ordinary room. The most common ISO classes are ISO 7 and ISO 8.
The old Federal Standard 209 (FS 209) includes these cleanroom classes: Class 100,000; 10,000; 1,000; 100; 10; 1. This standard was superseded in 1999 by ISO-14644-1. They were also withdrawn in 2001, but it is still used to some extent.
Cleanrooms must also follow industry-specific and regional standards. As mentioned, EU GMP (ABCD) applies to pharmaceutical products and USP (795, 797, 800, 825) to compounding pharmacies.
Below is an approximate comparison.
Particle count for clean room classification
The basis for cleanroom standards is micrometres, µm, which is the size of the particles to be filtered. As previously mentioned, cleanrooms are classified according to how clean the air is, according to the amount and size of particles per volume of air. The cleanroom classification table below shows the maximum concentration limits (particles / m3 of air) for particles equal to and greater than those shown.
Some classifications do not require certain particle sizes to be tested.
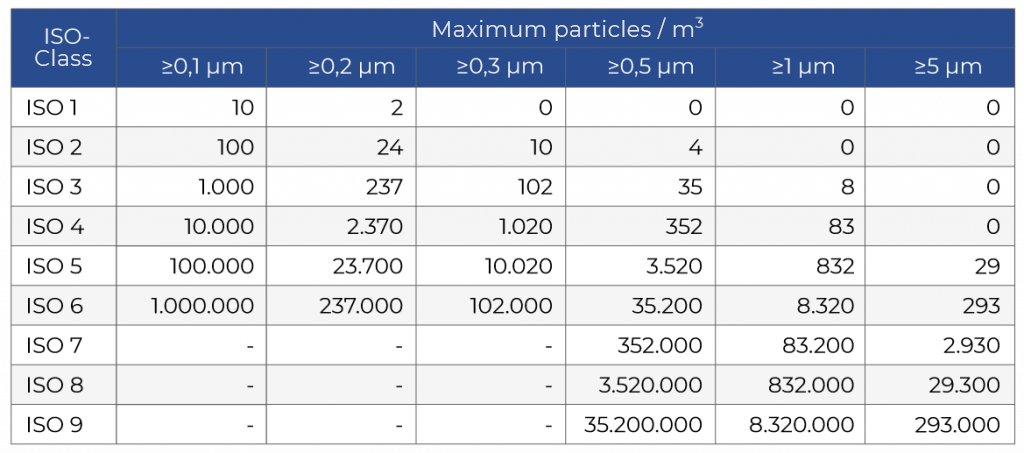
How to read the table::
For ISO 7, particles smaller than 0.5 µm are not taken into account. The concentration of particles ≥0.5 µm must be below 352,000, for particles ≥ 1 µm below 83,200 and for particles ≥ 5 µm below 2,930
In comparison, a typical office building or room in your house has somewhere between 18,000,000 and 36,000,000 airborne particles of 0.5 µm or larger, for every m3.
Air change per hour
Air purity is achieved by passing the air through HEPA and ULPA filters. The more often the air passes through HEPA filters, the fewer particles remain in the room air. The amount of air filtered in one hour divided by the room volume gives the number of air changes per hour. hour.
For GMP (A, B, C, D) it is a rule of thumb to apply:
- GMP D 5 – 10 air changes per hour
- GMP C 10-15 air changes per hour
- GMP B 20-25 air changes per hour
- GMP A 30-35 air changes per hour
Below is a table with a rule of thumb for air exchange with fine electronics.